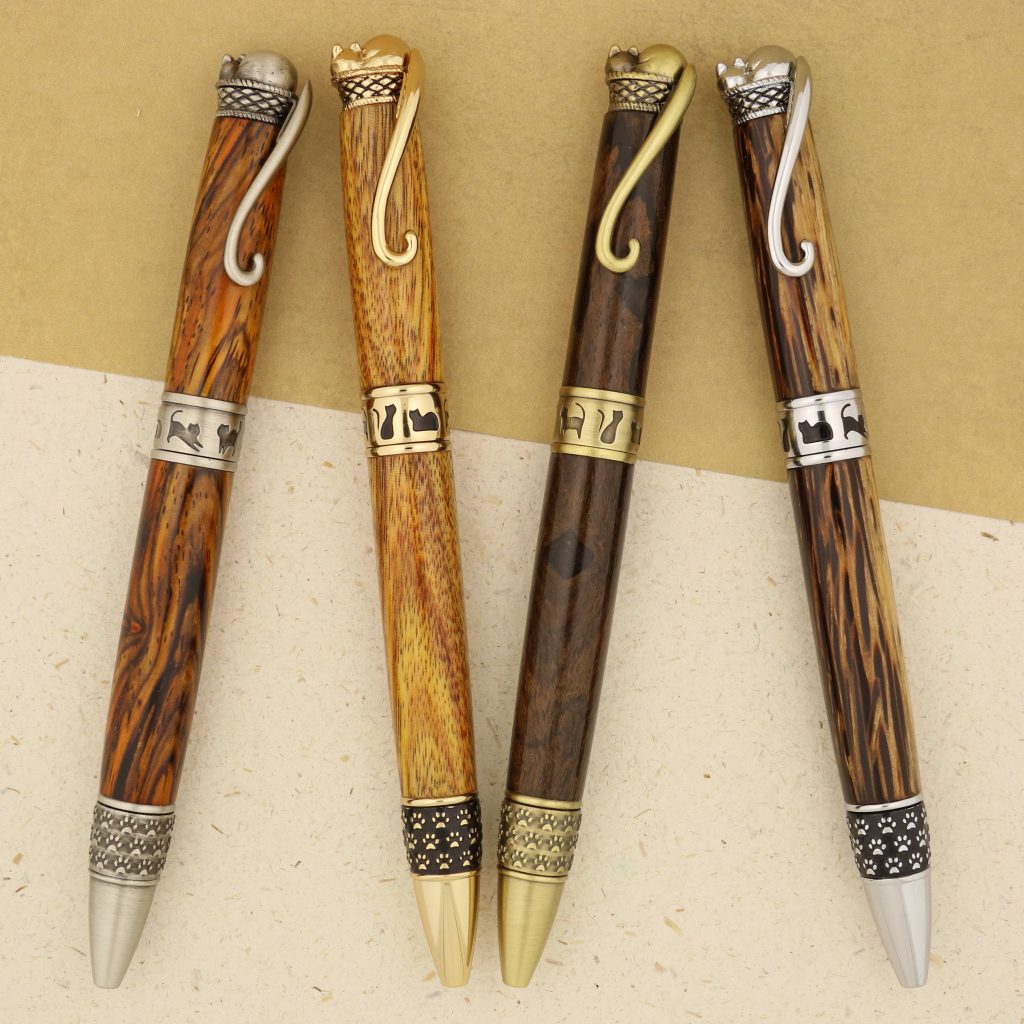
Wood-turned pens are much more than just a writing utensil. Often, they’re treasured gifts made from exotic wood and custom materials. Really, they’re works of art. That’s why there are some things you should do to ensure your special pen has a long life and continues to look beautiful. With all the ink refills and replacement parts available, there’s no reason you can’t use a prized pen for many years with some minor upkeep.
Preventing cracks and warping in pen turning
As a wood-turner, there are factors to consider from the very beginning that will prevent problems with a pen later on. Care needs to be taken from the time you select a blank to when you put the final finish on the barrels.
Climate Control. Start with dry wood that hasn’t been subjected to harsh, alternating weather conditions. In winter, consider keeping your exotic wood pen blanks near a humidifier to prevent shrinkage and in humid weather, try to store your wood indoors with climate control if possible. As wood goes through the cycle of hot and cold it shrinks and expands. The more this happens, the more prone to cracking and warping it becomes.
Stabilized wood. Stabilized wood has been specially treated to increase durability. During the stabilization process, the air is removed from the wood and replaced with resin. Once cured, the resin prevents moisture from entering the wood and interacting with its cell structure. It eliminates the problem of movement and swelling. Turning stabilized wood feels a little different than natural wood because of the resin content, but it makes for a very sturdy wooden pen, especially when dealing with burl or softwood.
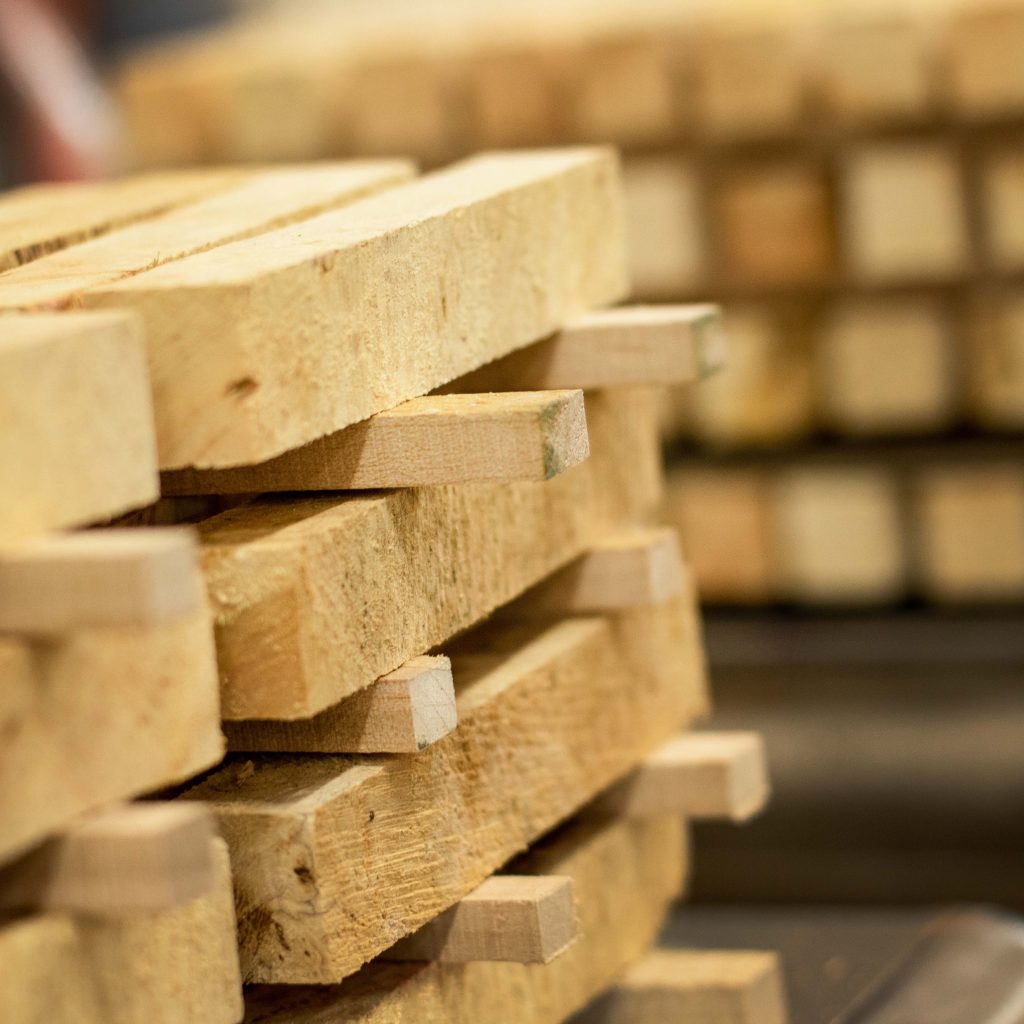
Waxed ends. You’ll notice when you purchase some pen blanks and spindles that the ends are covered in wax. This is a preventative measure to protect the exposed grain from moisture and dryness.
How to refinish a pen
Wood-turned pens will inevitably see some wear and tear over time. Sometimes the finish will become dull or scratched. One of the great things about wood is that you can usually refinish it to be as good as new.
Many oil or wax-based finishes are restorable, which means you can retreat the pen with the same product without sanding it down first, making it quick and easy. Other finishes, such as CA glue, require a little more effort.
- Disassemble your pen, preferably with an assembly/disassembly press.
- Using the original bushings, mount the barrels on the lathe.
- If you’re using a restorable finish, simply run the lathe on low speed, apply a few coats and you’re done.
- For a non-restorable finish, run the lathe at about 1500rpm and apply some abrasive polish such as EEE polish or Yorkshire grit. There should be plenty of friction to remove shallow scratches along with the existing finish.
- Stop the lathe and wipe the pen barrel. You will be able to see when the finish is coming off.
- Once the barrel is smooth, apply your finish of choice and reassemble your pen.
Storing wood-turned pens
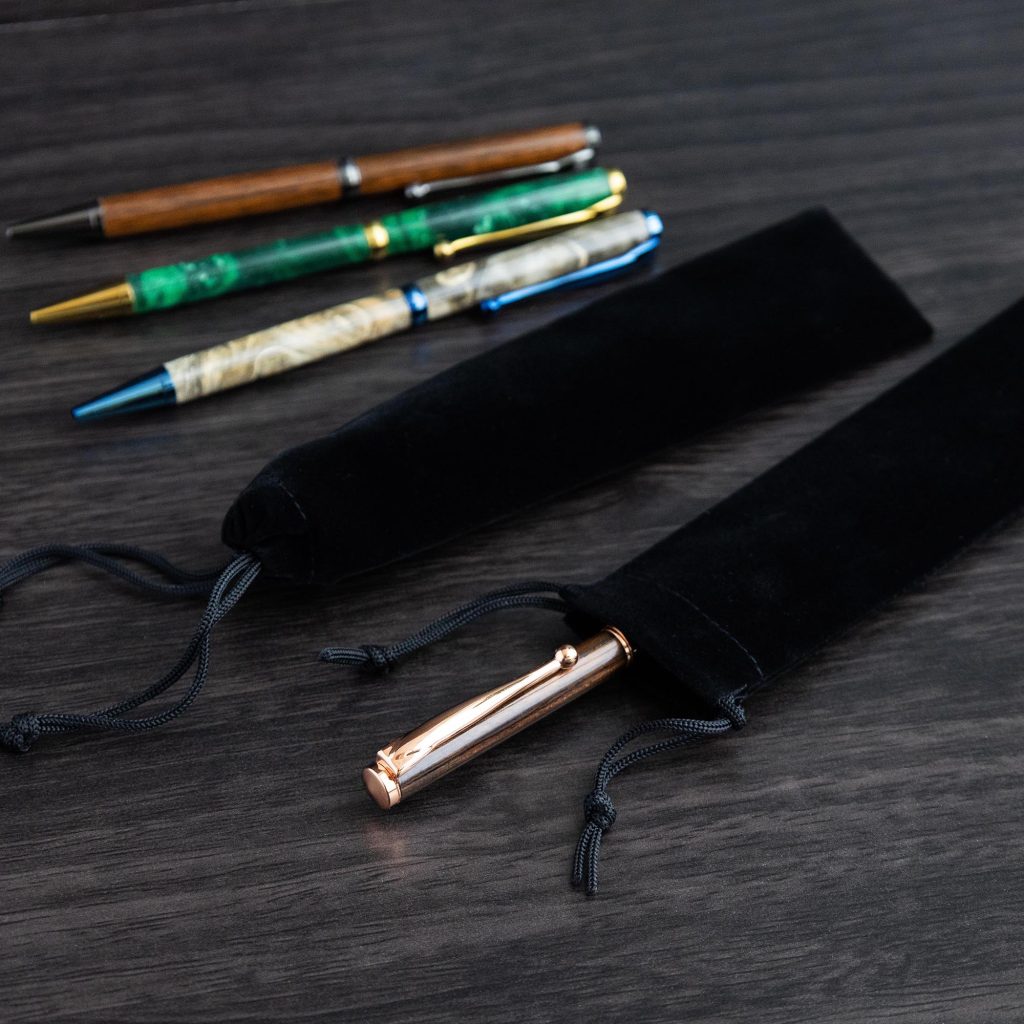
Even finished wood can respond to extreme temperatures, humidity and rough handling so it’s important to take care when storing your custom pens.
- Never leave your pens in a car, as this is where extreme heat and cold tend to occur.
- Don’t toss your pen in a drawer. It’s best to have pen boxes or, at the very least, a pouch store and protect it.
- Take care not to drop it. Even the best made pens can land in just the right way to crack. If you’ve followed other methods to prevent cracking it’s unlikely to happen, but better safe than sorry.
- Don’t leave your pens sitting in direct sunlight. The UV rays can deteriorate the wood fibres and in some cases, destroy the finish.
- Don’t clean your turned pens with harsh products or abrasives. They will ruin the finish and the wood.
- Consider specially made storage portfolios, especially if you’re selling pens at different markets and have to move them around. These padded fabric carriers are a handy way to transport and protect your goods.
A well-made custom pen can last a lifetime
Whether you’ve been wood-turning for decades or are just starting out, it’s important to treat your creations right from beginning to end. That means using quality wood, a good finish, decent storage options and a little maintenance. Get started at William Wood-Write. We have the top pen-making supplies and wood-turning tools to help you every step of the way — from the workshop to the craft market and into a lifetime of use.