Thanks to online shopping, there is a huge range of wood, resin and acrylic blanks for pen turning at your fingertips. The choices available for crafting custom pens are genuinely endless. But burl, exotic woods and synthetic materials each need to be approached differently to prevent blowout and get that perfect finish. Over the years, we’ve learned some tricks for turning different materials, ensuring our lathe projects look good and last a long time.
Turning durable burl pens
Burls are especially popular in the wood turning world because of their irresistibly unique design. The trouble with burl is that it’s inconsistent, containing both soft and hard spots as well as unexpected voids, knots or cracks. While these details are what make it so attractive, they can be difficult to turn and require special attention.
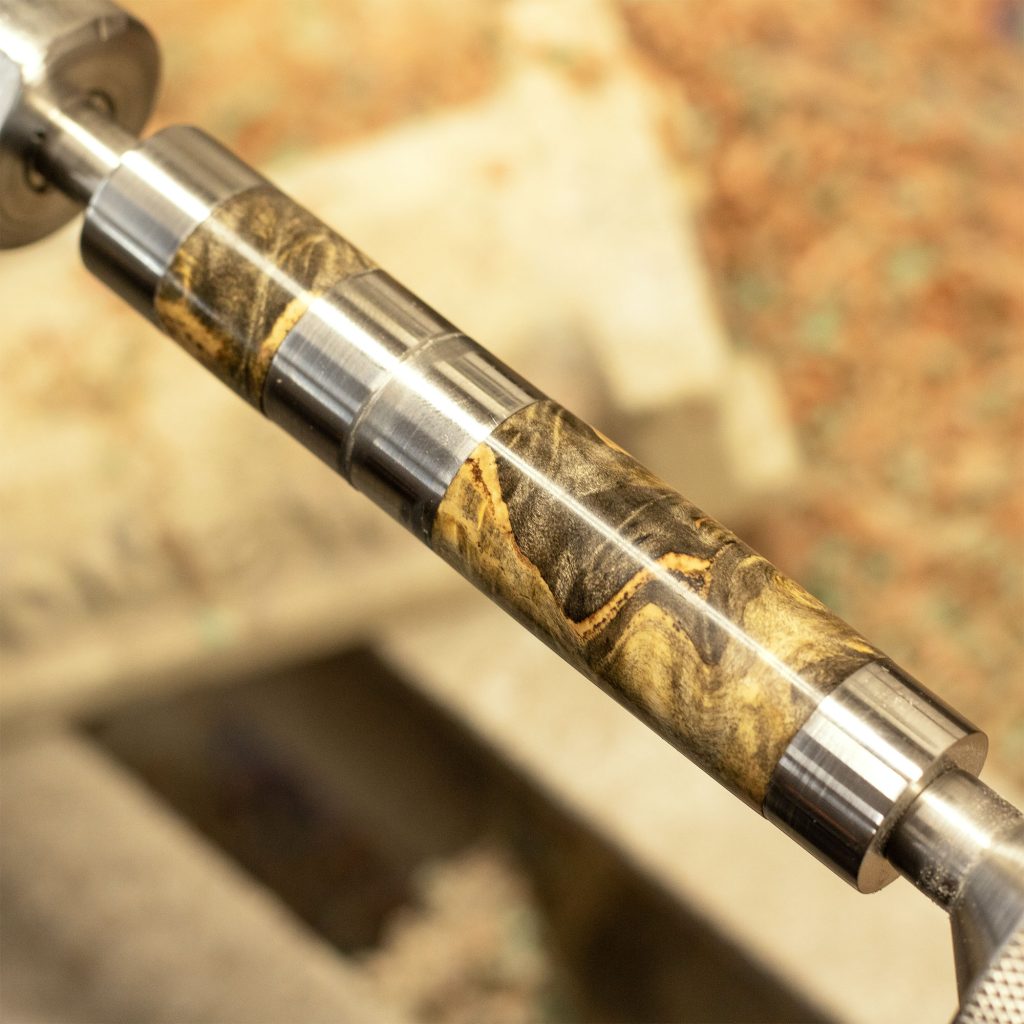
- Try CA glue. To strengthen sections of a burl pen blank that are especially soft or weak, apply some thin CA glue to the area. Thin CA glue will seep into the wood and stabilize it. CA glue can be used for other things as well, such as filling holes or cracks. It comes in clear, black and brown to either disguise or enhance these features, depending on the look you’re going for. Don’t forget to use an accelerator spray to help cure the glue and prevent a cloudy result.
- Go slow. When approaching the burl pen plank with your chisel, don’t rush. Go in slow and make small cuts. This way you can get a good feel for the inconsistencies, approach them accordingly and avoid gouging a soft spot. It might also have hard sections that can grab your chisel if you’re not careful.
- Use sharp tools. It’s general knowledge that the sharper your chisel the better when it comes to burl, but don’t forget that the drill bit you use should be ultra-sharp too. If not, you can end up with a crooked hole that’s too big for your tubes. Some pen makers start with a smaller drill bit, and slowly work up to a larger one of the right diameter.
Considerations for turning exotic wood pens
When turning pen blanks made from wood that isn’t burl, whether exotic or domestic, it’s best to choose your methods based on the wood itself. This includes factors like grain type, density and what kind of appearance you want.
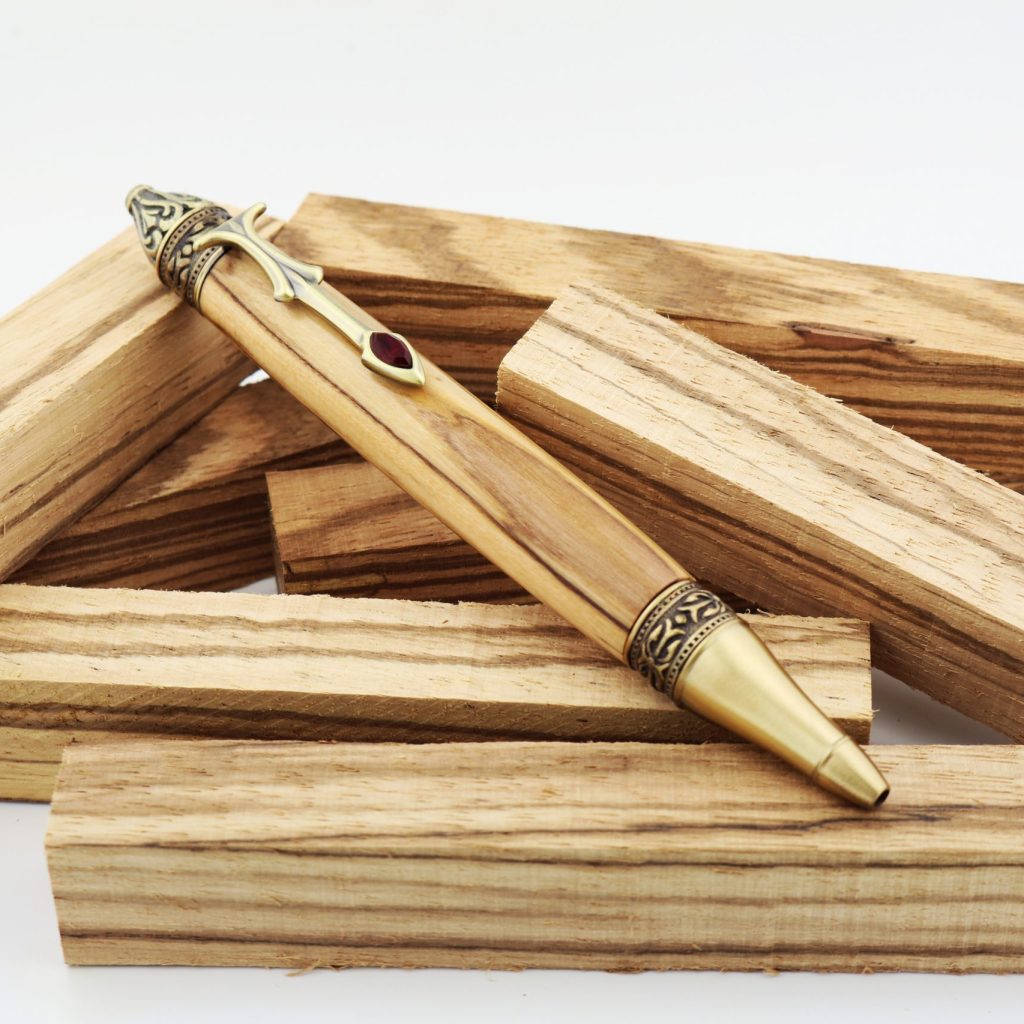
Grain Pattern. There are open and closed-grain woods. “Open grain” refers to hardwoods that have pronounced grain patterns, or figuring, caused by their growth cycle. They often have striking stripes and patterns like you see in zebrawood. Open-grained wood can be dense and slightly coarse to turn, with some parts more fibrous than others. Closed-grain woods like soft maple have little to no figuring. They tend to be softer, which means you can take bigger cuts. However, you should still go in slowly with sharp tools to avoid causing nicks and gouges.
Oiliness. Most domestic wood doesn’t have this problem, but when it comes to exotic wood for pen making, some species are known for emitting oils that can interfere with water-based finishes and glue. Bubinga, cocobolo, teak and other oily wood will repel finishes if untreated. To work around this, you can try wiping your turned pen blank with a solvent just before applying dewaxed shellac to seal it. Then, it’s a good idea to use a synthetic finish that’s not water-based.
Colour. If you’ve chosen to work with a brightly coloured wood, such as purpleheart, yellowheart or redheart, odds are you want to maintain that bright natural hue. Use a clear, UV-protective finish on any brightly coloured wood that you’d like to preserve. Avoid oils, waxes or finishes that are known for darkening wood, as these can change the colour of your pen. A good go-to is CA glue or a clear polyurethane finish.
How to finish a resin or acrylic pen
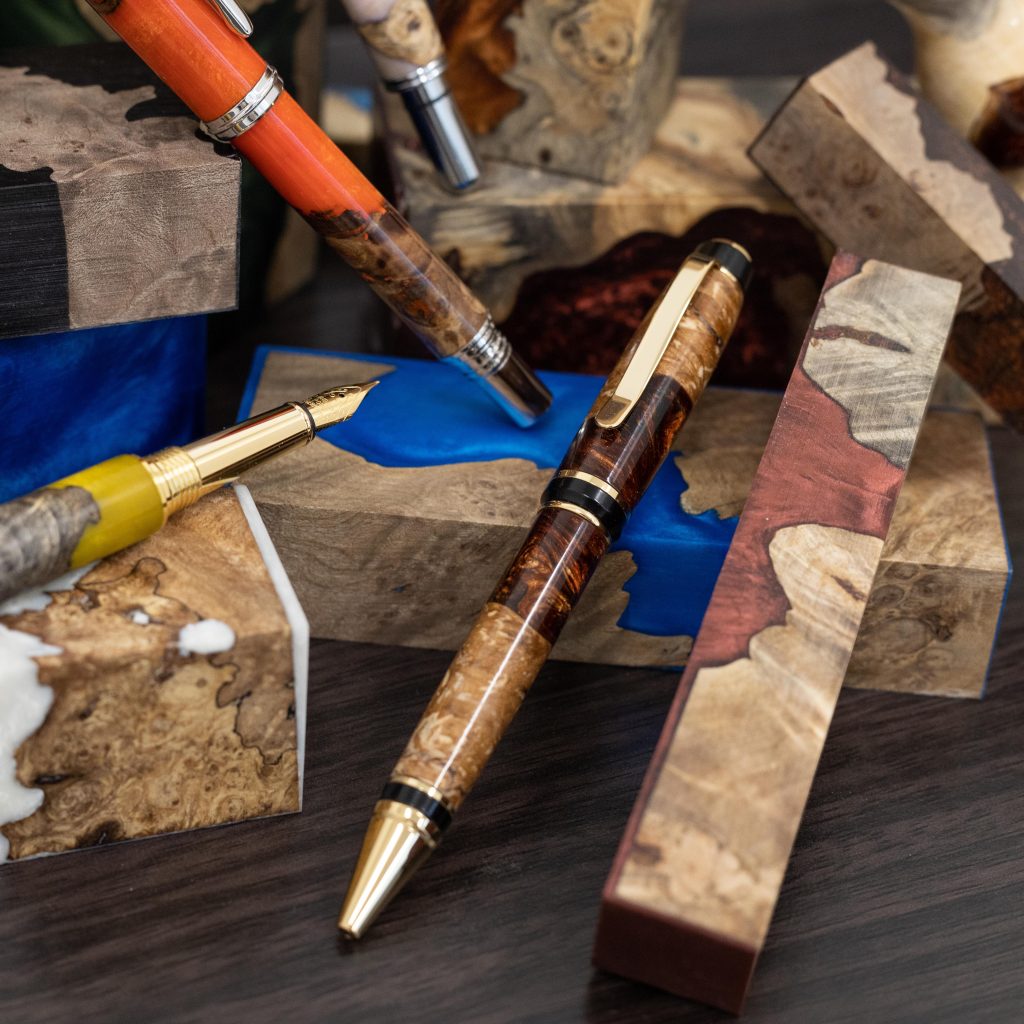
Turning acrylic and resin pens is a whole different ballgame. They can be brittle and chip easily, making them finicky to turn. A negative rake carbide cutter is a must. They also show scratches, especially the darker colours, and require more sanding and buffing. You also need to watch for heat when drilling or sanding because acrylic can melt.
When turning acrylic or resin, it tends to come off in “ribbons”. These can be messy and build up on the lathe, tangling around the mandrel. This is harmless, but you may have to stop every few minutes to pull them off. Aside from these details, the biggest difference is sanding and finishing, which requires a few extra steps to get rid of scratches.
- Once you’ve got your blank turned, slow the lathe down to about half speed.
- Start with the lowest grit of Abranet mesh and work your way up to the highest. Use light pressure and let the mesh do the work. Move the sheet around to different areas as you go to prevent heat. At this point, you will be able to see scratches running all around the circumference of the blank.
- Turn off the lathe, and using the same Abranet, sand sideways. Turn the lathe by hand, sanding side to side over the whole surface. Press a little harder for this, and try to make the vertical scratches disappear. Repeat with the other grits, taking your time and removing dust as you go.
- Select the lowest grit of micromesh and wet sand the pen barrel with water. Wet sanding will create a slurry, which is perfect for getting a flawless finish. Go through the micromesh grits up to 12000.
- Apply a small amount of Hut Plastic Polish to a clean shop cloth and spread it over the blank. Start the lathe and apply multiple coats for a hard shiny finish.
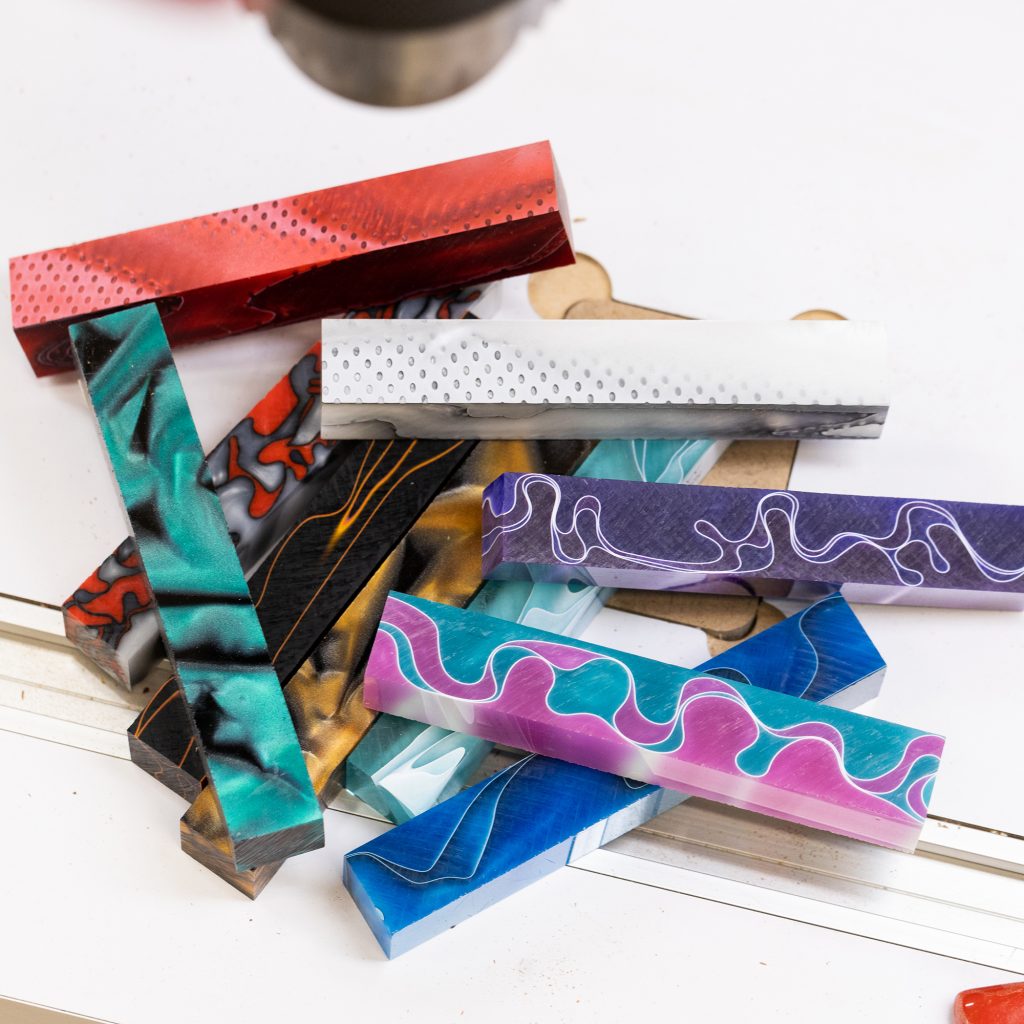
Increase your inventory with different materials for lathe projects
Whether you’re a burl enthusiast, an exotic wood fanatic or just love the sparkle and sheen of resin, there’s something for everyone. It’s sort of like every pen you make has its own personality! That’s why each one needs to be approached differently to get that customized, personal touch. Visit the William Wood-Write website to browse our huge selection of pen blanks, woodturning kits and tools for making magic on your lathe.